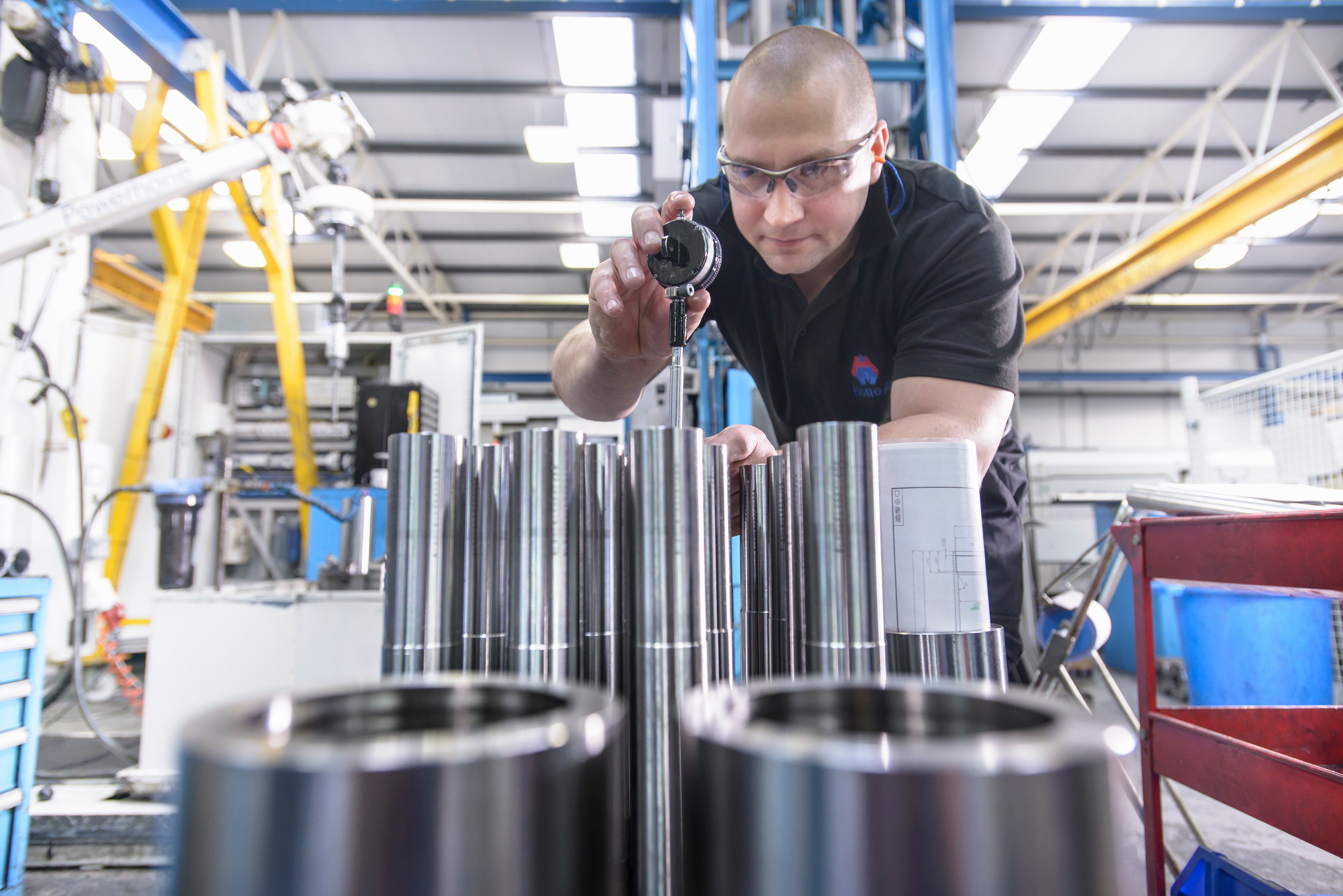
Manufacturers who operate in high-spec sectors, such as aerospace, automotive, and medical instruments, face constant pressure to deliver components that meet exacting dimensional standards – without compromising cost-efficiency or process reliability.Achieving high levels of internal surface accuracy, particularly for bores in engine parts, hydraulic systems, and aerospace assemblies, often exposes the limitations of conventional machining. In contrast, CNC honing offers a controlled, repeatable method for achieving superior geometric precision and surface quality.
Unlike CNC turning and milling, CNC honing removes minute amounts of material to correct imperfections left by earlier machining and achieve tolerances and finishes that other processes cannot consistently deliver. In this article, we’ll outline the key benefits of CNC honing in manufacturing.
1. High-Precision Geometric Correction
CNC honing excels at improving roundness, cylindricity, and surface finish. By applying a controlled abrasive action, it corrects distortions introduced during previous operations, which turning and milling alone cannot achieve. This makes CNC honing indispensable for parts such as valve bodies and hydraulic sleeves, where internal geometry directly impacts on performance.
2. Exceptional Surface Finish
The honing process produces a fine, crosshatched surface texture that is ideal for oil retention and reduced friction. This directly affects component efficiency and wear resistance, particularly in moving assemblies such as pistons or aerospace actuators. Improved surface finish can also reduce the need for additional treatments, helping to streamline production workflows. Alternatively, for components such as gas cylinders, a mirror type finish is required.
3. Tight And Repeatable Tolerances
CNC-controlled honing systems allow for micron-level accuracy with every pass. Automation ensures consistency across large batches, removing human variability and enabling manufacturers to meet quality standards reliably, which is especially important in industries governed by stringent regulations, such as Aerospace and Defence.
4. Extended Component Life And Reliability
The enhanced surface finish and precision geometry achieved by CNC honing directly translate to improved durability. In hydraulic or engine components, this means a lower risk of leakage, pressure loss or wear over time. For OEMs, the long-term performance gains of CNC honing often outweigh the modest investment during production.
5. Versatility Across Critical Industries
CNC honing supports a range of applications, from automotive brake and gear systems to aerospace bearing housings and high-pressure hydraulic components. Its ability to achieve fine finishes in tough materials - hardened steel or cast iron, for example - makes it a versatile and vital tool in precision manufacturing.
Need To Achieve Tighter Tolerances And Better Surface Finishes?
At Hone-All, we specialise in outsourced precision honing for complex, performance-critical components. All CNC honing is carried out in-house at our Bedfordshire facility by our own experienced team and never subcontracted. If we can’t help you, we will simply put you onto those who can...it’s all part of the service we provide to support out customers and the industry as a whole...
For a free quotation and expert guidance on your next project, please call our experts today on 01525 370666 or send us a message.